How to Report Issues with Spray Painting in NSW: Complaints Process
By:Admin
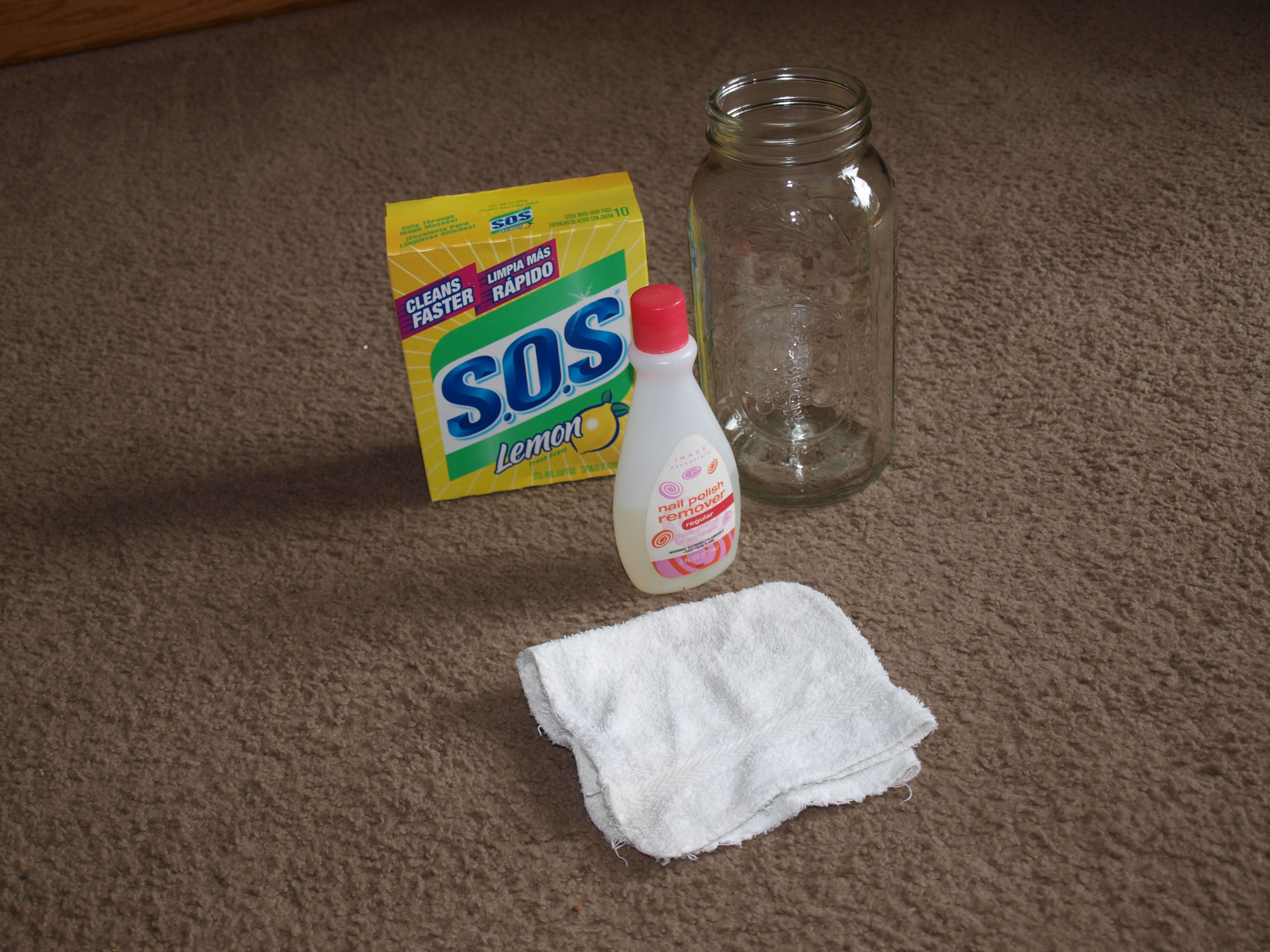
If you are experiencing overspray or fumes from spray painting, it's important to know where to turn for help. Fortunately, in New South Wales (NSW), you can report any issues with spray painting to the council.
When you notice it, you should first try and identify who is responsible for the spray painting work. You can speak with neighbours and local businesses nearby to see if they know who is doing the sprays. Once you have determined who is responsible for the spray painting, you can then contact the council and report the issue.
The council will then investigate the matter and take the necessary steps to prevent further overspray or fumes. This may involve issuing a fine or cease and desist order to the offender, or taking legal action against them if necessary.
It's important to report the issue to the council as soon as possible, as spray painting can have a significant impact on air quality and the health of residents in the area. Overspray and fumes can cause respiratory problems, headaches, and eye irritation. In extreme cases, they can even cause cancer and other serious health problems.
To avoid the negative effects of overspray and fumes from spray painting, it is important for businesses and individuals to take appropriate measures and use proper equipment. They should also follow the laws and regulations put in place by the government to protect the environment and the health of individuals in the area.
There are many different types of paint sprayers on the market, and it's important to choose a high-quality one that meets your specific needs. Whether you are a professional painter or a DIY enthusiast, the right tool can help you get the job done more efficiently and effectively.
In conclusion, if you are experiencing overspray or fumes from spray painting in your area, it's important to report the issue to the council. This will help ensure that the polluter is held accountable and that steps are taken to prevent further pollution in the future. By working together, we can help create cleaner, healthier, and more vibrant communities for ourselves and future generations to enjoy.
Company News & Blog
High-Quality Small Powder Curing Ovens from Chinese Manufacturers and Suppliers
A small powdercoating oven is an essential piece of equipment for businesses and DIY enthusiasts who want to achieve long-lasting, high-quality finishes on their metal and plastic projects. These ovens are designed to cure powder coatings by baking them onto the surface of the substrate, creating a durable and attractive finish that resists wear, corrosion, fading, and chipping.At Hangzhou Color Powder Coating Equipment, we offer a range of small powdercoating ovens that are perfect for small-scale projects, such as automotive parts, motorcycle frames, bicycle components, jewelry, and DIY home improvement projects. Our ovens are made with high-quality materials and components, ensuring reliable performance, fast heat up times, and even temperature distribution throughout the curing process.One of the key advantages of using a small powdercoating oven is the ability to achieve a professional-grade finish without the need for expensive spray booths or specialized equipment. With a small oven, you can easily apply powder coatings using a spray gun or electrostatic method, and then cure them in the oven for a few minutes to achieve a hard, durable finish.Another advantage of a small powdercoating oven is its energy efficiency. These ovens are designed to minimize heat loss and maximize heat retention, which means that they consume less energy and require less time to heat up and cool down. This translates into significant cost savings over the long term, especially for DIY enthusiasts who use the oven frequently.When choosing a small powdercoating oven, it's important to consider a few key factors, such as the size of the oven, the type of heating element, the temperature range, and the ease of use. At Hangzhou Color Powder Coating Equipment, we offer a variety of small powdercoating ovens to suit different needs and budgets, from basic models with manual controls to advanced models with programmable digital interfaces.Overall, a small powdercoating oven is an excellent investment for anyone who wants to achieve professional-grade finishes on their metal and plastic projects. With its energy efficiency, durability, and ease of use, this equipment can help you take your DIY hobby or small business to the next level.
Innovative Infrared Radiation Curing Technology for Powder Coating
Infrared Powder Coating: Innovation in Powder Coating TechnologyInfrared radiation curing powder coating technology is a game-changer in the world of industrial finishing. This revolutionary technique speeds up the curing process, reduces energy consumption and costs, and improves product quality and durability. In this blog, we’ll explore how infrared powder coating works, its benefits and applications, and its impact on the future of the powder coating industry.What is Infrared Powder Coating?Infrared powder coating is a process that uses infrared radiation to cure powder coating materials. Unlike traditional oven curing methods that require high temperatures and long baking times, infrared curing heats up the coating materials directly, resulting in faster and more efficient curing. Infrared radiation has a shorter wavelength and higher energy compared to traditional heating methods, such as convection or conduction, allowing it to penetrate the coating materials more deeply and evenly. This makes infrared powder coating ideal for complex shapes, large volumes, and sensitive products that require careful handling.Benefits of Infrared Powder CoatingThere are numerous advantages to using infrared powder coating, from improved productivity and reduced costs to enhanced quality and durability. Some of the key benefits of infrared powder coating include:1. Faster Curing Times: Infrared radiation quickly heats up the coating materials, which can reduce curing times by up to 75% compared to conventional ovens. This means faster processing times and increased throughput for manufacturers.2. Lower Energy Consumption: Infrared radiation uses less energy and requires lower oven temperatures than traditional heating methods, which can result in significant cost savings and lower carbon emissions.3. Improved Product Quality: Infrared radiation provides a more uniform and consistent heat source, which helps to eliminate defects such as pinholes, orange peel, and fisheyes. This leads to a higher quality finish that is more resistant to fading, chalking, and weathering.4. Enhanced Product Durability: Infrared powder coating creates a dense and uniform coating with excellent adhesion and corrosion resistance. This results in a more durable finish that can withstand harsh environments and heavy use.Applications of Infrared Powder CoatingInfrared powder coating is a versatile technology that can be used in a wide range of industrial applications, from automotive and aerospace to furniture and electronics. Some of the common applications of infrared powder coating are:1. Automotive Parts: Infrared powder coating is commonly used for coating car parts such as wheels, body panels, and frames. The fast curing times and enhanced durability of this technology make it ideal for automotive finishes.2. Metal Furniture: Infrared powder coating provides a durable and attractive finish for metal furniture, such as chairs, tables, and shelves. The technology's ability to handle complex shapes and large volumes is especially useful for mass production of furniture.3. Electronics: Infrared powder coating can be used to coat electronic components such as computer cases, circuit boards, and enclosures. Its uniform and consistent coverage can protect sensitive equipment in harsh environments.4. Aerospace: Infrared powder coating is widely used in the aerospace industry, where its durability, corrosion resistance, and low weight are essential. Its ability to handle large volumes and complex shapes make it a popular choice for aircraft and space vehicles.The Future of Infrared Powder CoatingInfrared powder coating is a rapidly growing technology that will continue to evolve and improve in the future. Innovations in infrared radiation sources, equipment design, and software control systems will enable faster and more precise curing of coating materials. Industry-wide adoption of infrared powder coating is also expected to grow, as more manufacturers recognize the benefits of this technology and seek to improve their production processes and product quality.In ConclusionInfrared powder coating is a game-changing technology that offers faster curing times, lower energy consumption, improved quality, and enhanced durability. Its versatility and flexibility make it ideal for a wide range of industrial applications, from automotive and aerospace to furniture and electronics. As this technology continues to evolve and improve, it will drive innovation and growth in the powder coating industry.
Build Your Own DIY Paint Spraying Booth in 9 Easy Steps
Building a DIY Paint Spraying Booth for a Safe and Clean WorkspaceWorking with aerosol cans, airbrushes, or high volume low pressure (HVLP) paint spraying systems requires a well-ventilated workspace to avoid inhaling fumes and overspray. Even if you wear a respirator, the risk of health hazards from toxic chemicals and particles cannot be completely eliminated. Besides, spraying paint in an open area can create a mess and ruin other surfaces that you don't intend to paint.That's where a homemade paint spraying booth comes in handy. By building a dedicated spray booth, you can contain the paint droplets and fumes in an enclosed space, capture them with a filter, and exhaust the air safely outside, leaving the surrounding area clean and free of contamination.Here are 9 steps to guide you through the process of building a basic paint spraying booth:1. Choose a locationFind a spot in your garage or workshop where you can fit the booth without blocking other objects or obstructing walkways. Ideally, the booth should be near an electrical outlet and a window or a vent to facilitate the exhaust.2. Measure and mark the size of the boothDecide how large you want the booth to be, based on the size of your workpieces and your available space. Use a tape measure and a straightedge to mark the outline of the booth on the floor. You can make it rectangular or square, but make sure it's at least 3 feet wide, 3 feet deep, and 6 feet tall to allow enough airflow and clearance.3. Frame the wallsUse 1x2 or 2x2 wooden studs to create the frame of the booth. Cut the studs to the lengths of your marked lines and assemble them using nails or screws. Make sure each corner forms a 90-degree angle and the frame is sturdy and level.4. Cover the walls with plastic sheetsAttach large sheets of clear plastic film or painter's plastic to the frame using staples or a staple gun. Make sure the plastic is taut and smooth, without any wrinkles or gaps. Leave one side open, which will be the entrance.5. Install a doorCut a slit in the plastic sheet for the entrance and attach a zipper or a flap to create a hinged doorway. Make sure it fits snugly and can be closed easily. You can also use magnets or velcro to secure the opening.6. Add lightingInstall a work light or a fluorescent tube light inside the booth to illuminate the work area. You can hang it from the ceiling or attach it to the frame. Make sure the light is bright enough and does not create shadows or glare.7. Insert a filter or exhaust fanTo remove the fumes and overspray from the booth, you can either use a filter or an exhaust fan. A filter is a mesh or fiber material that traps the particles and cleans the air, while an exhaust fan pulls the air out of the booth and directs it outside through a duct or a hose. You can choose either option depending on your budget and preference.8. Connect the exhaust to the window or ventIf you use an exhaust fan, connect the duct or hose to the window or vent that leads outside. You may need to drill a hole in the wall or use an adapter to fit the duct to the opening. Make sure the connection is tight and secure.9. Test and adjustBefore using the booth, turn on the fan or filter and spray some paint in the booth to see if it captures the overspray and fumes effectively. Adjust the position and power of the exhaust if necessary. Also, make sure to read the safety instructions of your paint system and wear appropriate protective gear such as gloves, goggles, and a respirator.By building a paint spraying booth, you not only protect yourself and your surroundings from harmful chemicals and mess but also increase the quality and consistency of your painting results. With a well-designed and functional booth, you can create a safe and clean workspace for your hobby or professional paint spraying needs.Keywords: paint spraying booth, DIY, aerosol cans, airbrush, HVLP system, fumes, overspray, respirator, toxic chemicals, particles, enclosed space, filter, exhaust, ventilation, plastic sheets, entrance, lighting, fluorescent tube, work area, fan, duct, safety.
Hollow Cone Spray Patterns: Styles, Angles, Flow Rates, and More!
and Spraying Systems Co.Hollow Cone Spray Nozzle: A Comprehensive GuideSpray nozzles play a critical role in various industries such as agriculture, automotive, and manufacturing. They are used to distribute liquids, gases, and powders uniformly and accurately over a specific area. One of the common types of spray nozzles is the hollow cone spray nozzle.This type of spray nozzle produces a hollow cone pattern with a ring-shaped impact area. It is designed to create a fine mist, making it ideal for liquid distribution applications that require finer droplets. The hollow cone spray nozzle is widely used in industries such as papermaking, steel manufacturing, cooling, and dust suppression.Types of Hollow Cone Spray NozzlesHollow cone spray nozzles are available in various styles, spray angles, flow rates, and materials. The most common styles of hollow cone spray nozzles include:Standard: This is the most common type of hollow cone spray nozzle. It produces a hollow cone pattern with a standard spray angle ranging from 30 to 120 degrees. The standard hollow cone nozzle is used in applications such as cooling, dust suppression, and humidification.Narrow angle: The narrow-angle hollow cone spray nozzle produces a smaller diameter spray pattern than the standard hollow cone nozzle. The narrow-angle nozzle is ideal for applications that require a high-impact spray such as cleaning and surface treatment.Wide angle: The wide-angle hollow cone spray nozzle produces a larger diameter spray pattern than the standard hollow cone nozzle. The wide-angle nozzle is used in applications such as humidification and evaporative cooling.Full cone: The full cone hollow cone spray nozzle produces a full cone pattern with a solid impact area. The full cone nozzle is used in applications such as gas scrubbing and fire protection.Spray AnglesThe spray angle of a hollow cone spray nozzle refers to the angle of the cone created by the nozzle's orifice. Spray angles can be specified by degrees, which ranges from 30 to 120 degrees for standard hollow cone nozzles. Narrow-angle nozzles have a spray angle ranging from 15 to 30 degrees, while wide-angle nozzles have spray angles ranging from 120 to 180 degrees.Flow RatesThe flow rate of a spray nozzle refers to the amount of liquid or gas that it releases per minute. The flow rate of hollow cone spray nozzles varies depending on the size and style of the nozzle. Generally, flow rates for hollow cone spray nozzles range from 0.1 to 1000 gallons per minute (GPM) for liquid applications and 0.1 to 300 cubic feet per minute (CFM) for gas applications.MaterialsHollow cone spray nozzles are made of various materials such as brass, stainless steel, and plastics like nylon and PVC. The choice of material depends on the specific application and environment where the nozzle will be used. For example, brass is a good choice for applications where corrosive liquids are used, while stainless steel is ideal for high-temperature applications.Spraying Systems Co. Hollow Cone Spray NozzlesSpraying Systems Co. is a leading manufacturer of spray nozzles, including hollow cone spray nozzles. Their nozzles are made of high-quality materials and designed to meet the specific needs of various industries.Spraying Systems Co. offers a range of hollow cone spray nozzles with varying spray angles, flow rates, and materials. Their nozzles are suitable for various applications such as cooling, dust suppression, humidification, gas scrubbing, and fire protection.ConclusionHollow cone spray nozzles are a crucial component in various industrial applications. They are designed to produce a uniform and accurate distribution of liquids, gases, and powders. The choice of nozzle depends on the specific application, and factors such as spray angle, flow rate, and material are essential considerations.Spraying Systems Co. offers a range of high-quality hollow cone spray nozzles for various applications. Their nozzles are made of durable materials and designed to meet the specific needs of their customers. Whether you need a standard, narrow-angle, wide-angle, or full cone hollow cone spray nozzle, Spraying Systems Co. has got you covered.
China's Leading Manufacturer Offers High-Quality Chain Conveyors for Various Applications
In today's fast-paced manufacturing industry, having a reliable and efficient material handling system is crucial for businesses of all sizes. One of the most widely used and trusted material handling solutions is the In-Floor Chain Conveyor. This conveyor system is ideal for transporting heavy loads over long distances, making it perfect for use in industrial settings.What Is an In-Floor Chain Conveyor?An In-Floor Chain Conveyor is a conveyor system that uses chains to transport heavy loads over long distances. It is designed to be installed flush with the factory floor, hence the name. The conveyor chain is usually made of steel and is driven by a motor that moves the chain along a track. The In-Floor Chain Conveyor can be used to transport a wide variety of materials, including boxes, pallets, and large industrial equipment.Advantages of In-Floor Chain ConveyorThere are several advantages to using an In-Floor Chain Conveyor. Firstly, it is an efficient and cost-effective material handling solution. This conveyor system is capable of carrying heavy loads over long distances, reducing the need for manual labor, and enabling fast and efficient movement of materials.Secondly, the In-Floor Chain Conveyor is an excellent space-saving solution. It is designed to be installed flush with the factory floor, freeing up valuable floor space for other equipment and activities. This system can also be customized to fit any factory layout, ensuring maximum efficiency and productivity.Thirdly, the In-Floor Chain Conveyor is a reliable and safe material handling solution. The chain is enclosed in a steel track, preventing any accidents or damage to the cargo. This system is also fully automated, reducing the risk of worker injury and ensuring consistent performance.Y&G Packing Machinery (Shanghai) Co., Ltd. - The Best In-Floor Chain Conveyor SupplierIf you are searching for a high-quality In-Floor Chain Conveyor for your manufacturing or industrial facility, look no further than Y&G Packing Machinery (Shanghai) Co., Ltd. Our company is a leading supplier of automated material handling solutions in China, offering a wide range of conveyor systems, filling machines, and sealing equipment.At Y&G Packing Machinery (Shanghai) Co., Ltd., we use only the best quality materials, components, and technology to manufacture our In-Floor Chain Conveyor. Our conveyor systems are designed to be durable, efficient, and reliable, ensuring maximum productivity and efficiency for your facility.Moreover, our In-Floor Chain Conveyor can be customized to fit your specific manufacturing needs. We offer a wide range of configuration options, including conveyor length, motor power, and load capacity. Additionally, our team of expert engineers can work with you to design a conveyor system that is tailored to your unique requirements.ConclusionIn conclusion, an In-Floor Chain Conveyor is an excellent material handling solution for any manufacturing or industrial facility. It is an efficient, space-saving, and reliable solution that can help improve productivity and reduce manual labor. If you are looking for a high-quality In-Floor Chain Conveyor supplier, look no further than Y&G Packing Machinery (Shanghai) Co., Ltd. Contact us today to learn more about our products and services.
Inexpensive Powder Coating Oven Made from Old File Cabinet
DIY Powder Coat Oven Door Seal: A Vital Component in Your Powder Coating SetupPowder coating has quickly become a popular method of applying a durable and uniform finish to metal parts. While it is a relatively simple process, there are specific requirements that must be met to achieve the desired results. One crucial component of any successful powder coating setup is a high-quality oven to cure the powder-coated parts.Commercial powder coat ovens can be expensive, with prices ranging from a few thousand dollars up to tens of thousands of dollars. Fortunately, with a bit of ingenuity and a few basic tools, you can build your own DIY powder coating oven at a fraction of the cost.The key to building a successful oven is to source a suitable enclosure that can withstand high temperatures and provide good insulation. For many DIYers, an old file cabinet or discarded refrigerator can work well. The next step is to add insulation materials like fiberglass or ceramic fiber blankets to improve the oven’s heat retention capabilities.Once you have designed and built the perfect oven enclosure, it’s time to focus on the smaller components that will make or break your powder coating results. One such essential element is the oven door seal. In this blog, we will discuss the importance of a good oven door seal and guide you through the process of making one for your DIY powder coating oven.Why You Need an Oven Door SealThe main purpose of a door seal is to keep the heat trapped inside the oven. You need the heat to cure the powder-coated parts properly. An ill-fitting or worn door seal can allow heat to escape, leading to uneven curing and poorly coated parts.Additionally, having a good seal creates a controlled environment inside the oven, preventing outside contaminants such as dust and debris from entering the oven and adhering to the newly coated parts.How to Make Your Own Oven Door SealTo make your own DIY oven door seal, you will need a few basic tools and materials:- High-temperature silicone- A caulking gun- Masking tape- A sharp utility knifeHere are the steps to follow:Step 1: Measure the Dimensions of Your Oven DoorUse a tape measure to accurately determine the dimensions of your oven door. You will need this information to calculate the length of silicone sealant you need for the job.Step 2: Apply Masking Tape to the Oven Door FrameProtect the areas around the oven door by applying masking tape to the edges of the oven frame. This will prevent the silicone from sticking to areas where it is not needed.Step 3: Apply the Silicone SealantLoad the high-temperature silicone into the caulking gun and apply a thin bead of silicone around the perimeter of the oven door frame, ensuring that it forms a continuous seal. Pay extra attention to the corners and areas where the door typically leaks heat.Step 4: Smooth the Silicone SealantUse your finger or a plastic spatula to smooth out the silicone sealant, ensuring that it fills any gaps or inconsistencies in the oven door. Take your time and be thorough in this step as it can significantly impact the effectiveness of the finished door seal.Step 5: Allow the Silicone to CureFollow the manufacturer's instructions for curing the silicone sealant. Typically, a high-temperature silicone sealant will require at least 24 hours of curing time.Step 6: Test Your New Oven Door SealAfter the silicone sealant has cured, remove the masking tape and close the oven door. Test the seal by running your hand around the door frame and feeling for any escaping heat.A DIY oven door seal made of high-temperature silicone is a cost-effective solution to ensure optimal heat retention and a controlled environment inside your powder coating oven. With a little bit of effort and some handy tools, you can create an effective oven door seal that will help you achieve the best possible results from your powder coating process. In summary, when building a DIY powder coating oven, the oven door seal is a vital component that cannot be overlooked. By following our guide and using high-temperature silicone, you can create a sturdy and reliable oven door seal that will last for years to come.
Kent Coach Company Gets a New External Spray Booth Installed by Todd Engineering
: Benefits for Coach CompaniesA high-quality external spray booth can make a world of difference for coach companies, not only in terms of the overall appearance of their vehicles, but also in terms of the efficiency and cost-effectiveness of their operations. In this blog post, we will take a closer look at the benefits that an external spray booth can offer to coach companies of all shapes and sizes, and how Todd Engineering is helping to meet the specific needs of its customers in this respect.First and foremost, an external spray booth can significantly enhance the visual appeal of a coach fleet, by providing a high-quality finish that is both durable and long-lasting. This in turn can help to boost brand recognition and customer loyalty, by creating a more professional and polished image that conveys a sense of reliability and trustworthiness.However, the benefits of an external spray booth go far beyond mere aesthetics. By providing a controlled environment for paint spraying, these facilities help to reduce the risk of paint contamination and other issues that can compromise the quality of the finish. This in turn can help to increase the lifespan of the paint job, by minimizing the risk of fading, peeling, or other forms of damage that can occur over time.Another major benefit of an external spray booth is that it can streamline the painting process, and make it more efficient and cost-effective for coach companies. By providing a dedicated space for painting, these facilities help to optimize the use of resources such as paint, materials, and labor. This in turn can help to reduce waste and increase productivity, by enabling more streamlined and effective processes that can deliver higher-quality results in less time.Of course, to fully realize these benefits, coach companies need to invest in high-quality external spray booths that are designed to meet their specific needs. That's where Todd Engineering comes in. With over 30 years of experience in the design and manufacture of spray booths, this company has established itself as a leading provider of customized solutions for a wide range of industries, including automotive, aerospace, and transportation.One of the key strengths of Todd Engineering is its ability to work closely with customers to create bespoke spray booths that are tailored to their precise requirements. From choosing the right size and layout, to specifying the materials, design features, and performance capabilities, Todd Engineering can help coach companies to optimize their painting processes and achieve the best results possible.This customer-centric approach is reflected in Todd Engineering's recent spray booth installation for Regent Coaches in Kent. By installing an external spray booth that is perfectly aligned with Regent Coaches' specific needs, Todd Engineering has helped this company to achieve a more professional, efficient, and cost-effective painting process that will enhance the overall quality and appeal of its vehicles for years to come.In conclusion, an external spray booth can offer numerous benefits for coach companies, ranging from improved visual appeal to enhanced durability, efficiency, and cost-effectiveness. By partnering with a trusted provider like Todd Engineering, coach companies can take advantage of customized spray booth solutions that are tailored to their unique needs, and designed to optimize their painting processes for maximum quality and value. Whether you are looking to enhance your brand image, reduce costs, or increase productivity, an external spray booth could be the perfect solution for your coach fleet.
Quality Spray Nozzles, Caps, Strainers, Nozzle Bodies & Clamps for Sprayers and Landscaping Equipment
article on the importance of quality spray nozzles in gardening, landscaping, and agriculture.Spray nozzles may seem like small and insignificant components of gardening, landscaping, and agricultural equipment, but they play a crucial role in ensuring the effectiveness and efficiency of various spraying applications. Whether you are irrigating your lawn, spraying fertilizers or herbicides in your crops, or beautifying your garden with pesticides, having high-quality spray nozzles can make a difference in achieving your desired outcomes.There are different types of spray nozzles available in the market, each designed to deliver specific spraying patterns, flow rates, and droplet sizes. Choosing the right spray nozzle for your application is critical in achieving optimal coverage and minimizing wastage of resources such as water, chemicals, and time. It is also important to consider factors such as the pressure and velocity of the liquid being sprayed, the type of surface being treated, and the environmental conditions in which the spraying is being done.One of the leading causes of spray nozzle failure is clogging, which can result from debris, sediment, or minerals in the liquid, or from the accumulation of deposits over time. Clogged spray nozzles can cause uneven spraying, reduced coverage, and increased maintenance costs. To prevent clogging, it is imperative to use high-quality strainers and filters that can trap particles as small as 5 microns and remove sediment and other impurities that can damage the nozzle. Regular cleaning and maintenance of spray nozzles are also essential in prolonging their lifespan and ensuring their performance.Another crucial factor in choosing spray nozzles is their material of construction. Low-quality nozzles made of inferior materials such as plastic or cheap alloys may wear out quickly, corrode easily, and result in frequent replacement. High-quality nozzles, on the other hand, are made of durable and corrosion-resistant materials such as stainless steel, brass, or ceramic, that can withstand harsh conditions, resist chemical attack, and maintain their shape and precision over time. Investing in high-quality nozzles not only prevents downtime and replacement costs but also improves the consistency and accuracy of your spraying applications.When it comes to choosing a supplier for your spray nozzles and related equipment, it is important to look for a reputable and experienced company that offers a wide range of products and services. A good supplier should be able to provide expert advice and support, fast and reliable delivery, competitive pricing, and customized solutions to meet your specific needs. They should also offer a comprehensive warranty and after-sales service to ensure that you get the most out of your investment and achieve maximum productivity and efficiency.In conclusion, spray nozzles may be small and simple components, but they are critical to the success of many spraying applications in gardening, landscaping, and agriculture. Choosing high-quality nozzles, strainers, and related equipment and partnering with a reputable and reliable supplier can help you achieve optimal coverage, minimize wastage and downtime, and increase productivity and profitability in your spraying operations.
Air Tools for Spray Painting - Find Affordable Options at Walmart.com
Spray Can Gun: The Ultimate Tool for Your DIY ProjectsAre you tired of using traditional paintbrushes for your DIY projects? Are you looking for a more efficient and effective way to paint your furniture or walls? Look no further than the Spray Can Gun!The Spray Can Gun is an innovative spray gun that allows you to spray paint or other liquid materials without the need for an air compressor. It is perfect for DIY enthusiasts, hobbyists, and professional painters looking for a portable and easy-to-use alternative to traditional spray guns.Advantages of Using a Spray Can GunThe Spray Can Gun offers numerous advantages over traditional spray guns and paintbrushes. Here are just a few benefits of using a Spray Can Gun:1. Easy to Use: The Spray Can Gun is incredibly easy to use. Simply attach the can to the gun, adjust the nozzle, and pull the trigger. You don't need to worry about hoses, compressors, or complicated equipment.2. Versatile: The Spray Can Gun can be used with a variety of materials, including paint, varnish, lacquer, and stain. You can use it to paint furniture, walls, or any other surface that needs a fresh coat of paint.3. Portable: The Spray Can Gun is lightweight and portable, making it ideal for DIY projects that require you to move around or work in confined spaces.4. Consistent Results: The Spray Can Gun delivers consistent and even sprays every time. You don't need to worry about drips, bubbles, or uneven coverage.How to Use a Spray Can GunUsing a Spray Can Gun is simple and straightforward. Here are a few steps to get you started:1. Choose the Right Can: Before you begin, make sure you choose the right can for your project. Different materials require different types of cans.2. Attach the Can: Attach the can to the Spray Can Gun by twisting it onto the bottom of the gun.3. Adjust the Nozzle: Use the nozzle adjustment to control the flow of paint or other materials. You can also adjust the nozzle to change the pattern of the spray.4. Test the Spray: Before you begin painting, test the spray on a piece of cardboard or paper to make sure it is working correctly.5. Begin Painting: Once you are ready, point the Spray Can Gun at the surface you want to paint and pull the trigger. Move the gun in a smooth, back-and-forth motion to ensure even coverage.ConclusionIf you are looking for a convenient and efficient tool to help you with your DIY projects, consider using a Spray Can Gun. With its ease of use, versatility, and portability, it is the perfect alternative to traditional spray guns and paintbrushes. So, what are you waiting for? Grab a Spray Can Gun and start your next DIY project today!
Effective Conveyor Systems for Powder Coating Paint Process
If you want to achieve a high-quality finish for your products, you need to invest in a reliable powder coating system. Powder coating is a durable and efficient finishing option that provides long-lasting protection for your products.However, to ensure that you get the best results, you need to choose the right powder coating conveyor system. At Pacline PACLINE, we have several conveyor types that have provided excellent solutions for handling products through the powder coating paint process.One of the most important components of a powder coating system is the oven. The oven is responsible for curing the coating on the surface of your products. This process requires careful control of temperature and time to ensure that each product receives a consistent finish.At Pacline PACLINE, we offer a range of oven powder coating conveyor systems that can handle a variety of products. Here are a few of our most popular options.1. Enclosed track conveyor systemsOur enclosed track conveyor systems are ideal for small to medium-sized products. The system uses a track that is suspended from the ceiling, allowing for excellent overhead clearance. This system is perfect for plants with limited floor space.Additionally, the enclosed design of the track helps to protect your products from contaminants. This feature makes it an excellent choice for powder coating applications.2. Power and Free conveyor systemsOur power and free conveyor systems are designed for maximum flexibility. These systems allow you to move products in any direction and at varying speeds. This feature makes it easy to customize the system to meet your specific needs.Additionally, our power and free conveyor systems can handle a variety of product shapes and sizes. This versatility makes it an excellent choice for plants with a wide range of products.3. I-beam conveyor systemsOur I-beam conveyor systems are designed for heavy-duty applications. This system can handle large, heavy products with ease. The I-beam design provides excellent strength and durability, making it an ideal choice for tough manufacturing environments.4. Overhead conveyor systemsOur overhead conveyor systems are perfect for plants with limited floor space. This system uses an overhead track to move products through the powder coating process. This design allows for excellent floor clearance, making it an ideal choice for small plants or plants with limited floor space.Our overhead conveyor systems can handle a variety of product shapes and sizes, making it an excellent choice for plants with a wide range of products.Regardless of the type of powder coating system you choose, it’s important to invest in a high-quality conveyor system. A reliable system will help you achieve a consistent finish on your products and ensure that your plant operates efficiently.At Pacline PACLINE, we have decades of experience designing, building, and installing conveyor systems for a variety of industries. We would be happy to work with you to design a system that meets your specific needs.If you’re interested in learning more about our oven powder coating conveyor systems, please don’t hesitate to contact us. Our team is dedicated to providing you with the best possible solutions for your manufacturing needs.